Plastic extrusion profiles in Melbourne refer to a shaped product which has various configurations. However, it does not include film or sheet products. It includes both solid and hollow forms. Though the extrusion technique appears to be complicated, it is a fairly simple process in reality.
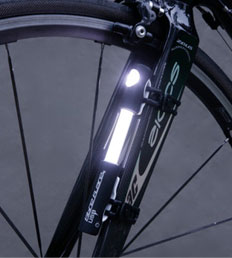
How does the Plastic Profile Extrusion Process Work?
The final goods often range from tubing, window frames to vehicle door seals that are largely manufactured through this process of plastic profiles. Items manufactured from continuous extrusion process include structural shapes (shower stalls, window frames, and channels), rods of various cross-sections, tubes, and pipes. O the other hand, some products, such as aluminium beverage cans, toothpaste tubes, and battery cases are manufactured from the discrete extrusion process.
The procedure of the plastic extrusion process involves melting, re-melting, and processing a kind of plastic. This entire technique is also referred to as thermoplastic resins. The latter ordinarily comes in pellets or beads which facilitates their deployment in the extrusion machinery. Once the raw material plastics are melted, they move to an area that meters it in preparation for the next phase.
The plastic materials usually get ready to be extruded into the die once it gets into the metering section of the machinery. It is the die that determines the shape that the plastic permanently transforms into. The raw material plastic is put into the die and a mandrel separates it.
Benefits of the Plastic Extrusion Process
• Coextrusion
The process of plastic extrusion includes numerous co-extrusion options. It essentially involves two or more extruders. With this process, multiple extruders feed the liquid molten plastic, however, at varying thicknesses and speeds to form a single extrusion head. It structures the materials into the required shape.
• Inherent Versatility
The plastic extrusion process is intensely versatile. It facilitates manufacturing products with complicated shapes and differing size, hardness, thickness, colour, and texture.
One of the most attractive features about the extrusion technique is that the process is still evolving though it has been around for a long time. Consequently, an established market player actively focuses on innovation. The constantly advancing contemporary world often brings in newer methods, materials, and technologies that benefit the process. Businesses strive to stay updated on the cutting edge of plastic technology to deliver the best final output to the customers.